Overview
a1-cbiss were approached by a trusted global food brand with a pizza production plant in Leyland, UK. The aim was to provide a low-cost gas monitoring solution for on-site Carbon Dioxide (CO2) trials.
The CO2 gas monitor was to be used during the dough proofing process to identify any potential CO2 dangers. The move would protect both the plant and personnel in the immediate area.
The Background
The factory takes responsibilty for maintaining safety standards. Numerous measures are taken to identify potential risks during the production process.
As part of the process, yeast is used to ferment the dough and maintain the freshness of the pizza dough.
However, when the yeast is left to prove, it chemically reacts to produce CO2 as a by-product. Commonly known for it’s asphyxiating properties and its ability to displace Oxygen, these levels of CO2 began to cause concern for the health and safety manager.
The Dangers of CO2
CO2 has a density that is heavier than air and collects in small toxic pockets low on the floor. It can build up in cellars and confined spaces. As CO2 is a mild asphyxiate, these pockets of CO2 can be hazardous to personnel.
At exposure levels above 5% vol, personnel will begin to feel fatigue to the point of exhaustion merely from respiration and severe headache.
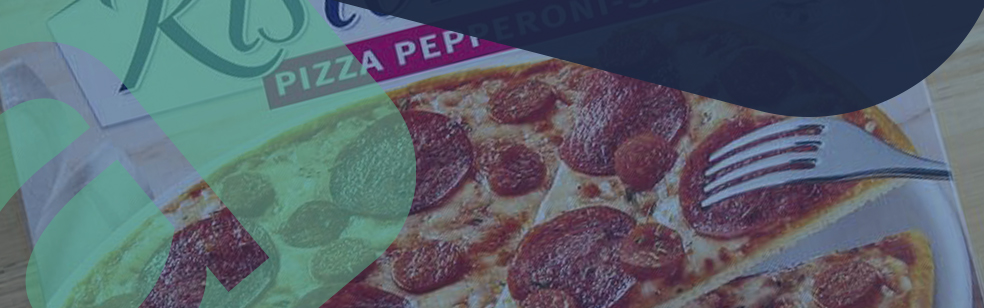
The Challenge
Due to the dangers presented by a build up of CO2, the health and safety manager decided to initiate trials to ascertain if the CO2 levels peaked those set by the EH40 guidelines.
The outcome of the trial would conclude if a fixed gas detection system was needed.
As the detector was only needed for initial trial phases, a1-cbiss had to be sure to provide a continuous gas data logger that could be left in-situ.
The Solution
After concluding a site survey, a1-cbiss provided the BM25 area monitor which monitors up to 5 gases. Conventiently, it offers over a reasonably lengthy period of time – up to 100 hours before a re-charge.
The BM25 was issued on a monthly hire, complete with CO2 sensor and data logging software/download cable. This enabled the health and safety manager to complete some testing in and around the Dough Prover and Waster Room areas to see what typical CO2 levels were.
The automatic recordkeeping and option to export records to view trends and metrics has been invaluable for the global food company and in particular for the Health and Safety Manager.
The success of the BM25 has since encouraged the production company to purchase their own BM25 from a1-cbiss.

Talk with the Experts
Contact us - Our team of application specialists can assist you with system design, installation, maintenance, and repair. As a systems integrator, we provide end-to-end support to ensure your facility has a reliable and effective gas detection system in place.
Sign up for more information - For more information on protecting your staff from the dangers of gas leaks, sign up for our emails.